Ultra Violet Lithography Process - Optics
A low-cost microscope projection photolithography system for high-resolution fabrication
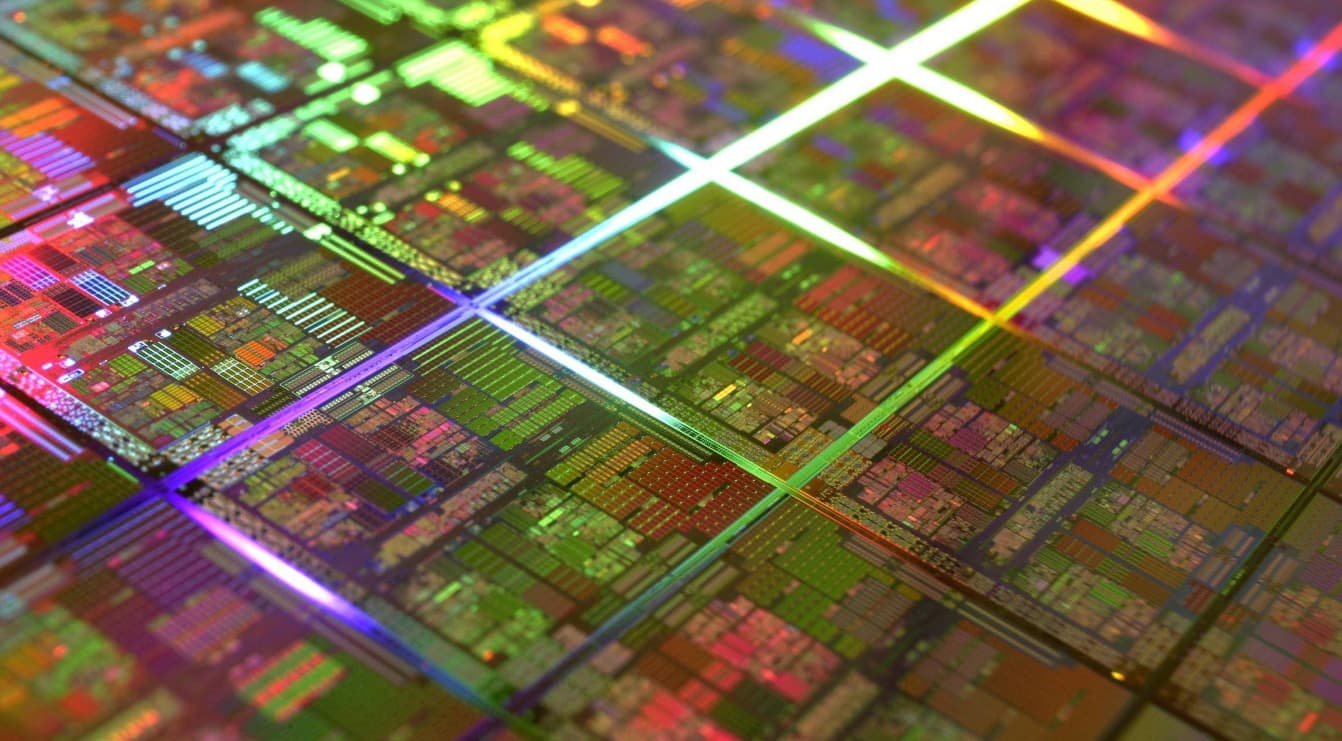
Overview
This project demonstrates a high-resolution UV projection system using a DLP470NE digital micromirror device (DMD) and a Nikon Plan Apo VC objective lens for sub-micron lithographic imaging. It is designed for applications that demand precision micro-patterning and optical lithography at near-diffraction-limited resolution.
Aims
- Implement a sub-micron lithographic projector system using a DLP chip and high-NA objective.
- Goal: Achieve 270nm projected pixel pitch at 405nm UV wavelength, with resolving power down to ~329nm.
- Target Application: Microscale fabrication, biomedical microstructures, and lab-on-chip prototyping.
System Specifications
DMD Chip
Property | Specification |
---|---|
Type | DLP470NE (0.47-inch 1080p DMD) |
Resolution | 1920 x 1080 |
Pixel Pitch | 5.4 µm |
Active Area | 5.832 mm (H) x 10.368 mm (W) |
DMD provides high pixel density with fast frame switching, ideal for maskless projection lithography.
Objective Lens
Property | Specification |
---|---|
Model | Nikon Plan Apo VC 20x |
Magnification | 20x Demagnification |
UV Correction | Up to 405 nm |
Numerical Aperture | 0.75 |
Working Distance | 1 mm |
Depth of Focus | 0.48 µm |
Field of View (FOV) | 1.25 mm diameter |
Theoretical Resolution | (0.61 x λ) / NA = 329 nm (λ = 405 nm) |
With a depth of focus of less than 0.5 µm, focus adjustment is critical for sharp feature transfer.
Projection Calculations
Projected Image Size
Using the 20x demagnification from the objective:
- Projected Height: 5.832 mm / 20 = 0.292 mm
- Projected Width: 10.368 mm / 20 = 0.518 mm
- Diagonal: √(0.292² + 0.518²) ≈ 0.354 mm
This falls well within the 1.25 mm field of view provided by the objective.
Pixel Size and Resolution
- Projected Pixel Size: 5.4 µm / 20 = 270 nm
- Objective Resolving Power: 329 nm @ 405 nm
- Resolution Gap: 329 - 270 = 59 nm resolving mismatch
Projected pixel size is below the diffraction-limited resolution, meaning some features may not resolve cleanly due to the NA and wavelength limits.
Summary Table
Parameter | Value |
---|---|
Projected Image Size | 0.292 mm x 0.518 mm |
Projected Pixel Size | 270 nm |
Diffraction-limited Res. | 329 nm (at 405 nm wavelength) |
FOV of Objective Lens | 1.25 mm diameter |
Working Distance | 1 mm |
DOF (Depth of Focus) | 0.48 µm |
Alignment and Wafer inspection
In UV lithography, precise alignment between layers is critical to ensure that patterns are correctly printed onto the wafer. Misalignment can lead to circuit failure or reduced yield. Prior to photoresist exposure, CMOS cameras are often used in combination with microscopes and alignment marks to achieve high-precision alignment between the silicon wafer and the photomask.
CMOS Inspection/Alignment camera
Property | Specification |
---|---|
Sensor | CMOS 21 Megapixels KP-2307V |
Lens Mount | C-Mount |
Zoom | Supports upto 7x Digital Zoom |
Output Interface | HDMI/USB |
Max. Resolution | 6112 x 3440 |
Techniques and Tips for Using CMOS Sensors in UV Lithography Alignment
Lighting and Contrast Enhancement
Use collimated UV/visible light at oblique angles to enhance topographic features and alignment marks. Implement ring lights or coaxial illumination for even lighting without shadows. Use polarizers to reduce glare and improve contrast between metal layers and silicon substrate.
Calibration and Focus
Perform daily calibration of the camera sensor to correct for geometric distortions. Use auto-focus routines based on contrast or sharpness algorithms for rapid wafer focusing. Adjust the working distance and numerical aperture of the objective lens to match the desired resolution and depth of field.
Image Processing Techniques
Utilize edge detection algorithms (e.g., Canny, Sobel) to clearly define alignment marks. Apply histogram equalization to enhance contrast in low-dynamic range lighting. Use template matching to automatically find and align reference marks across multiple wafers.
Mechanical Stability
Mount the camera on a vibration-isolated stage to prevent motion blur during inspection. Ensure the wafer chuck is stable and free of particles to avoid z-height misalignments.
Digital Zoom & ROI Optimization
Use digital zoom judiciously: while it helps with visualization, it does not improve optical resolution. Define Regions of Interest (ROIs) for faster image processing and alignment tracking.
Integration with Alignment Software
Pair the CMOS camera with lithography alignment software that supports sub-micron correction using image feedback. Use machine vision libraries (OpenCV, Halcon, etc.) for custom alignment algorithms.